AWARDS FINALIST: Methanex – Investing in new distillation technology to reduce emissions
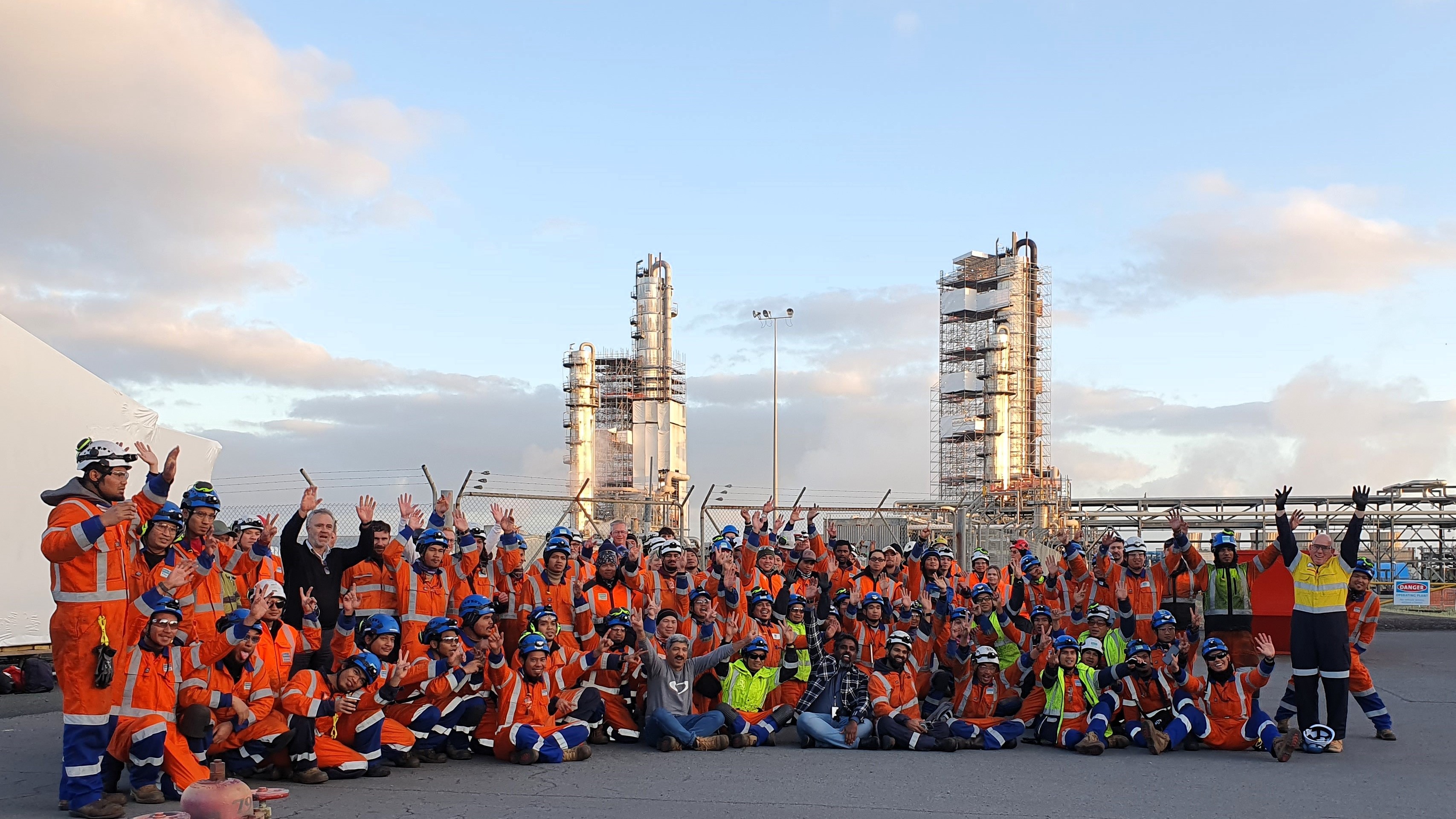
An upgrade of Methanex’s two distillation columns at its Motunui site will save up to 50,000 tonnes of carbon dioxide emissions a year.
The complex project, completed in late 2023, involved redesigning and replacing 88 distillation trays in the near 30-year-old columns to improve control of the flow of gas and liquid within them.
The improved energy efficiency from the retrofit boosted the plant’s distillation capacity by 25 per cent, allowing Methanex to decommission its third distillation column at the Waitara Valley plant, thereby consolidating operations and further reducing emissions.
Methanex says close collaboration among the project partners was key to its success.
After extensive evaluation, detailed front-end engineering design began in February 2022.
Design
Engineering consultancy Koch-Glitsch designed the new trays using advanced software modelling to optimise hydraulic performance and contact efficiency. The meticulous design and manufacturing process required the coordination of parts from multiple countries, including Italy, Malaysia, China, and Australia.
The 88 trays comprise more than 370,000 components and filled fifteen 40-foot containers.
Executing this complex project within a tight 60-day maintenance window required strict scheduling and posed numerous challenges, including working at heights in the 70-metre-high columns, managing confined spaces and dealing with the challenging winter winds of Taranaki.
Dialog Fitzroy and Cunningham Construction managed the work on the ground, including erection of a 102-tonne scaffold tower with a purpose-built lift to facilitate safe and efficient access to the distillation columns.
Methanex says a key initiative was the creation of a life-sized model of a distillation column segment, allowing the 95-strong installation crew to practise in a controlled, low-risk environment. This innovative training approach ensured precision and safety during the actual installation, which involved assembling 240,000 components within the columns’ narrow confines.
Lessons
Adopting early lessons also provided big benefits.
The project team saw an opportunity to modify the scaffold design so that the renewal of a protective coating on the columns could be done in parallel with the refit, avoiding the need to dismantle and rebuild scaffolding and reducing costs for both projects.
A review of the 24/7 shift structure – with rostered days off – used on the first column also delivered productivity gains. Going instead to a six-day pattern kept crews together during the week and also during a shared rest day. Labour costs on the second column were 46 per cent lower per tray.
The project team, a mix of local and international contractors, came together to celebrate Matariki with the wider Methanex team. The project’s multicultural workforce was also supported through various initiatives, such as the establishment of a temporary mosque on the site so Muslim crew members could observe their religious practices.
Financially, the project was a triumph, coming in close to 10 per cent under budget and completed ahead of schedule.
Methanex says the successful integration of local businesses in scaffolding, logistics and other areas also generated substantial economic benefits for the wider community.
The Large Energy User Initiative of the Year category is sponsored by EECA.