AWARDS FINALIST: Mataura Valley Milk – Project Recharge - High Pressure Electrode Boiler
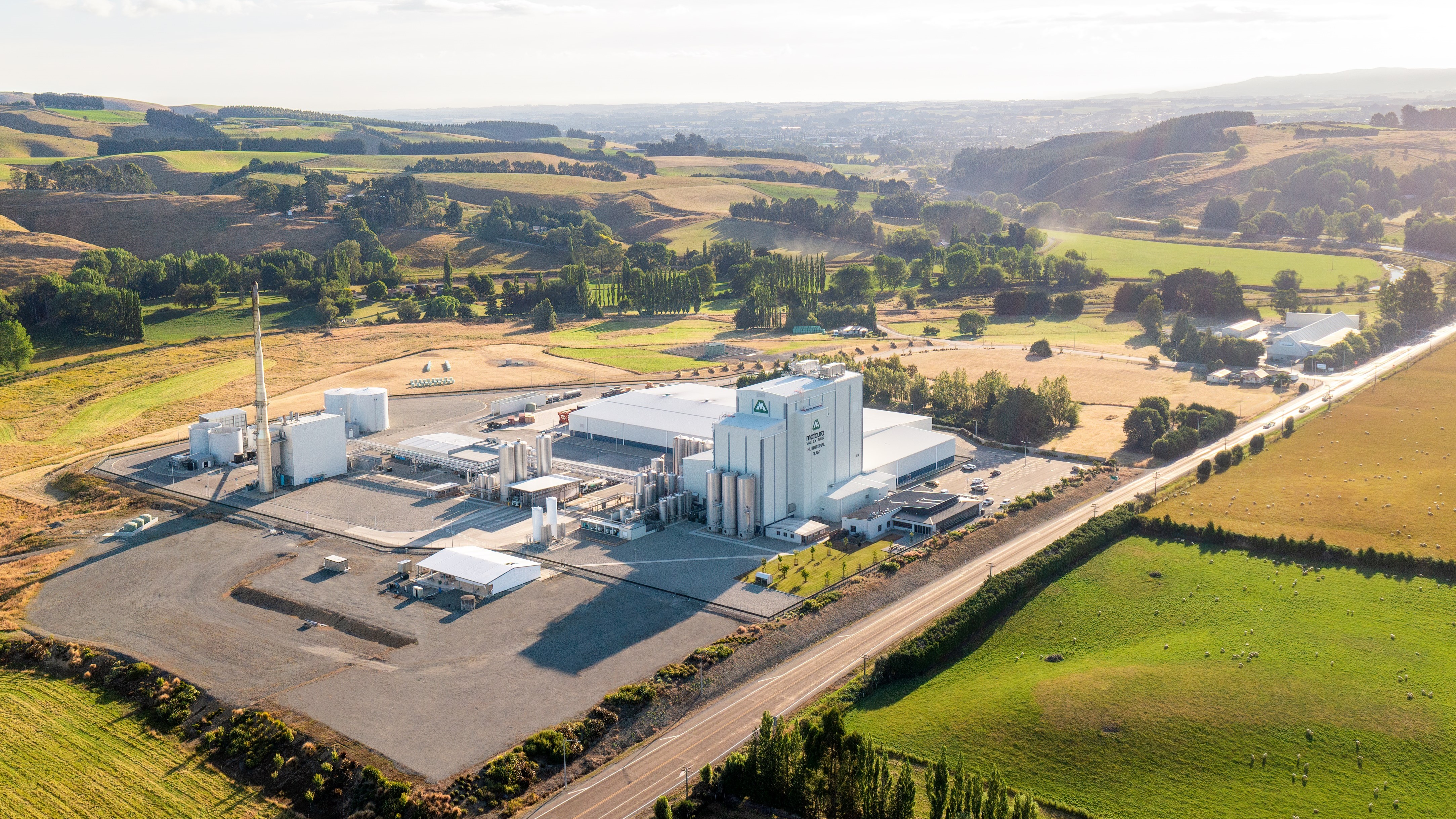
Mataura Valley Milk's Project Recharge has reduced the company’s emissions by about 22,000 tonnes a year and demonstrated an effective role for high-pressure electrode boilers in dairy processing.
The pioneering decarbonisation project, supported by the Energy Efficiency and Conservation Authority, started concept work in early 2021, when the company was expecting to convert its lignite boiler to biomass.
But an Energy Transition Accelerator study undertaken with EECA and engineering consultancy Aurecon showed electrification was also feasible.
Using low-pressure electric boilers – supplying 10 barg/180 degree steam – as two other dairy companies have, would have only displaced about 30 per cent of Mataura Valley’s coal use.
High-pressure
The firm instead opted to use a high-pressure boiler – supplying 40 barg/250 degree steam – using technology unproven in New Zealand, and offsetting 100 per cent of its coal use.
With a conditional $5 million grant from EECA’s former GIDI fund, Project Recharge formally kicked off in September 2021.
The electrode boiler is much more efficient than combustion boilers, with a thermal efficiency of about 99 per cent against 80 per cent.
But the firm and its contractor, Windsor Energy, needed to overcome a range of technical challenges to deliver what is a first of its kind for the New Zealand dairy industry.
Redesign
Swedish boiler maker Elpanneteknik redesigned the electrode insulator specifically for the dairy industry’s demanding requirements, and to reduce the known risk of seal failure.
Windsor also needed to redesign its boiler offering, coming up with several improvements, one of which was a new high-voltage switch-gear design, to allow the boiler to cope with the industry’s “winter shut” during which time it would need to run at minimum load frequently cycling on and off.
Mataura Valley says standard switchgear would fail in a short timeframe, by exceeding the rated number of cycles. The project team identified a cost-effective solution rated for 30,000 cycles and fitted with a replaceable HV switch module.
A safety review also identified a risk if an operator accessed the boiler's top access platform without isolating the high-voltage power supply which feeds in at the same point. A trapped key system, which interlocks with the power supply, was installed and is now a standard fixture on similar boiler designs here.
Water supply
The boiler also requires ultra-pure de-mineralised water to operate safely and efficiently. The company had to first upgrade its bore water supply and then needed to replace its existing ion-exchange de-mineralisation unit with a significantly more complex reverse osmosis and electro-deionisation unit.
Mataura Valley, part of The a2 Milk Company, says the improved water supply meant the new water treatment plant could be reduced in size. Masons Engineers, the successful tenderers, were then able to offer units small enough to fit within an existing building, achieving a “significant” cost saving.
That proved critical as the project was challenged by building sector inflation. Pivoting the plan so that the new boiler also shares some water pre-heating assets with the existing plant produced further savings without compromising on project deliverables.
Significant upgrade
Mataura Valley says the total project took two years and also included a significant upgrade at Transpower’s Gore GXP, and PowerNet’s McNab substation. PowerNet’s supply to the plant was also upgraded to 33 kV from 11 kV.
The new plant was commissioned towards the end of 2023. The company is currently looking at options to put the coal-fired boiler into long-term storage in order to future-proof the site’s demand response options.
The Large Energy User Initiative of the Year category is sponsored by EECA.